Engineering and Design of Military Ports - indexEngineering and Design of Military Ports - ufc_4_159_020001Unified Facilities Criteria (UFC) - ufc_4_159_020002Foreword - ufc_4_159_020003Engineering and Design of Military Ports - ufc_4_159_020006Figures - ufc_4_159_020008Tables - ufc_4_159_020009Chapter 1 Introduction - ufc_4_159_020010Chapter 2 Port Site Selection Physical and topographical featuresTable 2-1. Diameter of Berth (in Yards) Using Ship's Anchor and ChainTable 2-2. Diameter of Berth (in Yards) Using Standard Fleet Moorings, Telephone BuoyTable 2-3. Diameter of Berth (in Yards) Using Standard Fleet Moorings, Riser ChainChapter 3 Layout of Harbor FacilitiesBreakwatersFigure 3-1. Use of offset breakwater heads to shelter entrance.Berthing basinsChapter 4 Site Investigation Hydrographic and topographic surveys.Figure 4-1. Unified soil classification. Topographic surveysChapter 5 Coastal ProtectionWaves and wave pressuresDesign wave calculationFigure 5-1. Wave Characteristics.Figure 5-2. Deepwater wave forecasting curves (for fetches of 1 to 1,000 miles).Figure 5-3. Deepwater wave forecasting curves (for fetches of 100 to more than 1,000 miles)Figure 5-4. Forecasting curves for shallow-water waves (constant depth = 5 feet).Figure 5-5. Forecasting curves for shallow-water waves (constant depth = 10 feet).Figure 5-6. Forecasting curves for shallow-water waves (constant depth = 15 feet).Figure 5-7. Forecasting curves for shallow-water waves (constant depth = 20 feet).Figure 5-8. Forecasting curves for shallow-water waves (constant depth = 25 feet).Figure 5-9. Forecasting curves for shallow-water waves (constant depth = 30 feet).Figure 5-10. Forecasting curves for shallow-water waves (constant depth = 35 feet).Figure 5-11. Forecasting curves for shallow-water waves (constant depth = 40 feet).Figure 5-12. Forecasting curves for shallow-water waves (constant depth = 45 feet).Figure 5-13. Forecasting curves for shallow-water waves (constant depth = 50 feet).Chapter 6 Pier and Wharf LayoutTransit shed.Roll-on/roll-off ramps.Highway facilities. The port should have accessFigure 6-1. Types of pier and wharf layouts.Figure 6-2. Various widths of apron for different operating conditions.Chapter 7 Live-Load RequirementsLongitudinal loads.Chapter 8 Structural DesignSubstructure designFuture expansion - ufc_4_159_020050Figure 8-1. Open Type Wharf Construction with Concrete Relieving Platform on Timber Piles.Figure 8-2. Open-Type Wharf Construction with Concrete Relieving Platform on Steel Pipe Piles.Figure 8-3. Open-Type Wharf Construction with Concrete Relieving Platform on Concrete Pile.Figure 8-4. Open-Type Wharf Construction with Concrete Relieving Platform on Caisson Piles.Figure 8-5. High Level Open-Type Wharf Construction with Concrete Deck on Timber Piles.Figure 8-6. High-Level Open-Type Wharf Construction with Concrete Flat Slab Deck on Steel Pipe Piles.Figure 8-7. High-Level Open-Type Wharf Construction with Concrete Deck on Steel Pipe Piles.Figure 8-8. High-Level Open-Type Wharf Construction with Concrete Deck on Precast Prestressed Concrete Caissons.Figure 8-9. High-Level Open-Type Wharf Construction with Precast Concrete Deck on Concrete Piles.Figure 8-10. High-Level Open-Type Wharf Construction with Concrete Deck on Prestressed Concrete Beams-Steel Pipe Piles.Figure 8-11. Solid fill-type wharf construction with steel sheet pile bulkhead.Figure 8-12. Solid fill type wharf construction with steel sheet pile bulkhead and relieving platform anchor.Figure 8-13. Solid fill-type wharf construction with circular steel sheet pile cells.Figure 8-14. Solid fill-type wharf construction with cellular steel bulkheadFigure 8-15. Solid fill-type wharf construction with reinforced concrete crib wharf.Figure 8-16. Timber deck structure.Figure 8-17. Typical expansion joint detail.Chapter 9 Fender SystemsRubber-in-compressionTable 9-1. Pneumatic Fenders for Military UsesSelection of fender system type.Design procedure. - ufc_4_159_020072Design procedure. - ufc_4_159_020073Table 9-3. Energy to be Absorbed by Fenders Pile fendersTable 9-4. Comparative Merits of Different Construction Materials in Energy-Absorption CapacityFigure 9-1. Timber pile-fender systems.Figure 9-2. Energy-absorption characteristics of conventional timber pile fenders.Figure 9-3. Hung timber fender system.Figure 9-4. Typical retractable fender systems.Figure 9-5. Resilient Fender System (spring rubber bumper).Figure 9-6. Resilient Fender System (rubber-in-compression).Figure 9-7. Load-Deflection and Energy-Absorption Characteristics Figure 9-8. Load-Deflection and Energy-Absorption CharacteristicsFigure 9-9. Load-Deflection and Energy-Absorption CharacteristicsFigure 9-10. Resilient fender system (rubber in shear) by RaykinFigure 9-11. Load-deflection and energy-absorption characteristics - ufc_4_159_020087Figure 9-11. Load-deflection and energy-absorption characteristics - ufc_4_159_020088Figure 9-12. Typical Lord flexible fender systems.Figure 9-13. Load-deflection and energy-absorption characteristics of Lord flexible fender.Figure 9-14. Rubber-in-torsion fender.Figure 9-15. Yokohama Pneumatic Rubber Fenders (jetty and quay use).Figure 9-16. Yokohama Pneumatic Rubber FendersFigure 9-17. Yokohama Pneumatic Rubber FenderFigure 9-18. Yokohama Pneumatic Rubber FendersFigure 9-19. Suspended fender.Figure 9-20. Resilient fender system (dashpot).Figure 9-21. Floating camel fenders.Chapter 10 Mooring DevicesFigure 10-2. Plan and elevation views of a corner mooring past.Figure 10-4. Typical chocks.Figure 10-6. Typical power capstan.Figure 10-8. Typical layout of mooring devices.Chapter 11 Dockside Utilities for Ship ServiceFigure 11-1. Typical water-supply connection in deck of pierChapter 12 Cargo Handling FacilitiesUsing floating equipmentTable 12-1. Characteristics of Various Commercially Available Cranes.Figure 12-1. Burton system.Figure 12-2. Typical heavy duty, rubber-tired gantry crane.Figure 12-3. Typical rail-mounted gantry crane.Figure 12-4. Fixed derrick.Figure 12-5. Container off-loading through the use of crawler-mounted crawFigure 12-6. Crane capacity.Chapter 13 Container PortsTypes of container operations.Figure 13-1. Recommended container storage and marshaling areaAppendix A References - ufc_4_159_020118Appendix B Surfacing Requirements for Container Storage and Marshaling AreasContainer handling vehicles.Thickness requirements for flexible pavements.Table B-1. Design Criteria Restrictions (200-10,000 Passes)Table B-2. CBR and Thickness Requirements for 200 and 10,000 Passes Table B-3. Design Criteria Restrictions (200-50,000 Passes)Table B-4. CBR and Thickness Requirements for 200, 10,000, and 50,000 Passes Figure B-1. LARC LX.Figure B-3. Clark 512.Figure B-5. Hyster H620BFigure B-6. LeTro-Porter 2582.Figure B-8. Travelift CH 1150.Figure B-9. P&H 6250-TC.Figure B-10. LeTro Crane GC-500.Figure B-11. M52 Tractor-trailer.Figure B-12. CBR required for operation of aircraft on unsurfaced soil.Figure B-13. Flexible Pavement Design Curves for LARCLX (amphibian).Figure B-14. Flexible Pavement Design Curves for Shoremaster (straddle carrier).Figure B-15. Flexible Pavement design Curves for Clark 512 (straddle carrier).Figure B-16. Flexible Pavement Design Curves for Belotti B67b (straddle carrier).Figure B-17. Flexible Pavement Design Curves for Hyster H620B (front-loading forklift)Figure B-18. Flexible Pavement design Curves for LeTro-Porter 2582 (front-loading forklift).Figure B-19. Flexible Pavement Design Curves for Lancer 3500 (side-loading forklift).Figure B-20. Flexible Pavement Design Curves for Travelift CH 1150 (yard gantry).Figure B-21. Flexible Pavement Design Cure for P&H 6250- TC(mobile crane).Figure B-22. Flexible Pavement Curves for LeTro Crane GC-500 (mobile gantry crane).Figure B-23. Flexible Pavement Design Curves for M52 Tractor and Trailer (truck-trader combination)Bibliography - ufc_4_159_020146
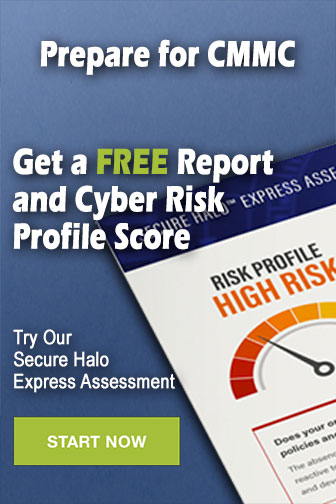